Projects
Tile Grout Filling Conveyor
Project Details
Moyr SEC were approached by an OEM to program and commission a machine that would unpack buckets, convey them, fill them, weigh them and palletise them. The programming and initial setup was to be carried out locally, with commissioning being carried out at the End User site. A detailed operation of the machine was discussed and logged with the OEM. Programming and testing was carried out successfully at the OEM site. Once the machine was fitted at the EU, full commissioning was carried out with the OEM personnel on hand. During this time, additionally functionality was requested by the EU and added by the OEM, which lead to alterations to the original operating code.
Project Outcome
The project was a success and fully automated the procedure for the EU. A stack of buckets were conveyed to the starting point, once detected, the top bucket was removed by the machine and placed on another conveyor, this bucket was moved to filling section, where the bucket was filled to the top with the product. Once filled, the bucket was conveyed to the weighing section to check the contents weight. Providing this is correct, the bucket is passed down the line, to the lid fitting area and then on to the end of the conveying area, where the bucket is removed by a robotic arm and placed on a pallet. When enough buckets have been placed on the pallet, the pallet is automatically wrapped with plastic film and moved to the storage area.
Scope
- PLC progaaming – Mistubishi
- HMI Programming – Mitsubishi
- Servo Programming – Mitsubishi
- Integration with the weigher
- Integration and programming of the Robot Arm.
- Onsite alteration made at commissioning in accordance with the customer design change.
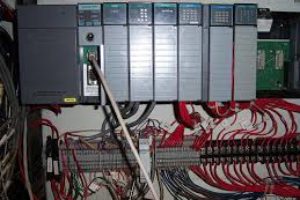
Food and Beverage • Cake Machine
Project Description:
Moyr SEC was approached to design a system to control a multi-layer cake baking machine. The machine consisted of multiple conveyors which produced a continuous baked cake. The operator entered the number of cakes per minute required. This number was used to calculate the speed of the conveyors, which determined baking time by changing the transit time through an oven. The speed information was sent to multiple VSDs to change the speed of conveyors. The speed control had to be accurate enough to prevent the tearing or bunching of cake as it transitioned between conveyors and as the multiple layers were brought together. VSDs with feedback were used to obtain the required accuracy. The cake was then delivered to a cutter to divide the cakes into the correct size.
Project Outcome:
The old VSD system was hard to adjust since each VSD needed to be individually adjusted. With the new system, VSDs were adjusted based on operator’s input which allowed for less downtime when the line was changed for different products. As a result, a significant increase in product throughput.
Technology Replaced:
- Old VSD System
New Technology Applied:
- PLC Progamming Allen Bradley SLC 500
- HMI Programming Allen Bradley PanelView
- VSD Programming Allen Bradley.
- Incorporation of safety circuits Allen Bradley.
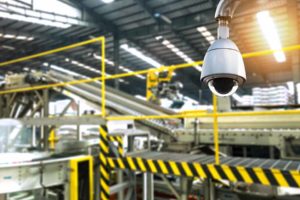
CCTV and Access Control – Indoor and Outdoor
Project Details
CCTV is a valuable tool in the fight against crime and also as a way of monitoring that correct saftey and operating procedures are being carried out correctly. This project had an existing CCTV system in place, with several different IP cameras fitted at various locations. However, only the important cameras were still functional and there were many areas which weren’t covered by any cameras.
An assessment was made to establish where cameras were needed and where power supplies needed to be installed. It was decided that cameras were needed externally from end to end, so wireless transmitters were used to carry the signals back the main building. A number of other IP cameras were fitted throughout the inside and outside of the building via POE switches.
At key areas and entry points, hardware sensors were fitted and alarm signals taken back to the NVR to trigger actions within the CCTV system. New monitors and PTZ controllers were fitted in the control room with a high security internet connection for remote viewing. New access control swipe devices were fitted at various locations and integrated with the CCTV system.
Project Outcome
The company now have full coverage of all areas regarding local or remote viewing. The two PTZ cameras have super zoom facilities that can focus in on a specific area with incredible detail. Even if a vulnerable area isn’t being viewed by an operator at that specific moment, the alarm integration will draw their attention to it immediately. Details of a dedicated alarm monitoring service were passed on to the company to give them 365/7/24 response cover.
Existing System
Several IP cameras, in various states of functionality.
New System
- Damaged cables replaced
- New IP cameras
- POE switches added
- Wireless Ethernet 500m
- Swipe card readers added
- Two high spec PTZ’s
- New monitors/Controls
- Web connected with alarms
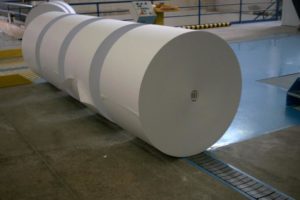
Conveying • Material Handling System
Project Description:
Moyr SEC designed a system to deliver 400 to 1600 pound rolls of paper to printing presses using an in-floor chain conveyor. The system consisted of carts holding rolls of newspapers that traveled through the press room until a press operator needed a roll of paper; at which time the operator pressed a button diverting the new roll to the press. At the press the roll was removed, the empty cart detected and sent back to an area where it could be refilled. Filled carts were automatically merged back onto the main line. Special carts were used to remove waste such as the roll covering and empty spools. Full waste carts were diverted to the waste area, emptied, and automatically merged back to the main line. The critical functions included controlling the cart stops at the merge area and implementing a shutdown if a collision was about to occur at the merge point.
Project Outcome:
The implementation of the system reduced cart collisions thereby increasing operational safety and allowing quicker reloading of the presses.
Scope:
- PLC Programming Allen Bradley ControlLogix
- HMI Programming Allen Bradley PanelView Plus HMIs
- VSD Programming Allen Bradley
- Various panel components (Pilz, Scheider, Phoenix)

Conveying • Pneumatic Conveying Systems
Project Description:
Moyr SEC designed controls for multiple baghouse systems and hydrated lime injection systems used at multiple coal-fired power plants. The hydrated lime system had multi-point injection points and was used with fluid bed boilers. Hydrated lime is a proven alkaline reagent used to remove SO3 from the flue gas. Both pressurized and vacuum conveying was implemented. Blower motors, feeders, and rotary airlocks were controlled and monitored. Alarm conditions were monitored and control interlocks utilized allowing the system to operate safely.
Project Outcome:
Systems provided an effective and cost-efficient way to reduce emissions from the fluid bed boilers. The use of control interlocks and alarm monitoring kept the systems operating safe and increased the equipment’s performance.
Scope:
- PLC Programming Allen Bradley ControlLogix
- HMI Programming Allen Bradley PanelView Plus HMIs
- Motor Control – Schneider
- Various Panel components (Pilz, Scheider, Phoenix)
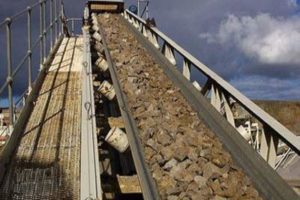
Conveying • Scarfing / Crusher Conveyor System
Project Description:
Moyr SEC designed a crusher conveyor control system to replace an existing relay panel. The system consisted of conveying material through a series of conveyors and hydraulic crushers. Crushed material was then conveyed and separated by size and conveyed to different piles. Speed of the conveyor was controlled by VFD based on operator input. Safety interlocks were applied to prevent any possibility of injury. The system was able to operate in automatic, remote and manual modes. HMI displayed alarm conditions and location of fault events.
Project Outcome:
The combination of the PLC and HMI provided a more modernized system which increased throughput and minimized downtime while meeting all safety requirements.
Technology Replaced:
- Antiquated Relay Panel
New Technology Applied:
- PLC Programming Mitsubishi
- HMI Programming Mitsubishi
- Motor Control Schneider
- Various Panel Components (Schneider, Pilz, Wago)
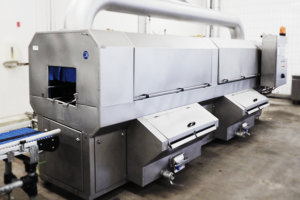
Specialist Bottles – Industrial Network
Project Description
All the plant machinery was to be networked back to a central location for control and data collection. To achieve this, a common network solution had to be installed and the machine control components programmed and connected to it. This involved updating a lot of the components, adding new hardware to them and in some cases, a complete swap out with a modern PLC including the re-writing of the program.
Project Outcome
The new network was installed and the relevant hardware to connect to it. The require machinery are now connected to the network, which allows the desired control from a central location and automatic collection of data. This ensures the company now have faster and more accurate record keeping and can manage the flow of production more easily.
Scope
- Network installation
- PLC Programming (Various)
- HMI Programming (Various)
- DataCom Programming
- Hardware Installation
- Panel Wiring
- Access Control Installation